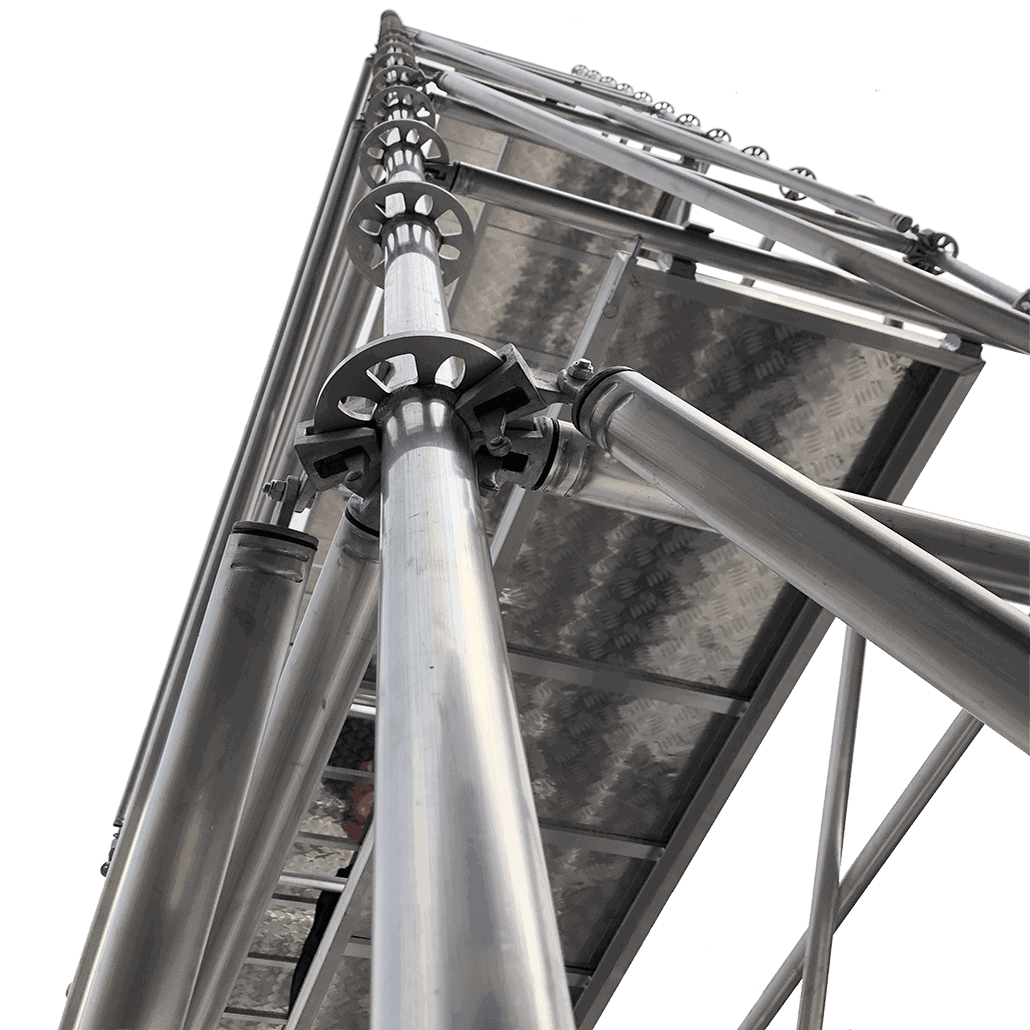
- Higher Initial Cost: Aluminum scaffolding is generally more expensive than steel scaffolding. This higher upfront cost can be a significant factor for projects with tight budgets or those that require extensive scaffolding.
- Lower Load Capacity: Although aluminum is strong relative to its weight, it does not support as heavy loads as steel scaffolding. This limitation makes it less suitable for heavy-duty construction work and projects that require lifting heavy equipment or materials.
- Vulnerability to Damage: Aluminum is softer than steel, making it more susceptible to dents and damage if not handled carefully. This can affect the long-term structural integrity of the scaffolding if it is frequently moved or subjected to rough conditions.
- Limited Height and Reach: Aluminum scaffolding typically cannot reach the same heights as steel scaffolding, which can be a disadvantage for projects requiring high elevation access, such as high-rise buildings or bridges.
- Limited Availability: In some regions, aluminum scaffolding may not be as readily available as steel scaffolding. This can pose logistical challenges and potentially increase costs if materials need to be sourced from distant suppliers.
- Repair Limitations: If aluminum scaffolding becomes distorted, it may not be as easily repaired as steel scaffolding, which can impact its longevity and cost-effectiveness over time.
Table of Contents
Aluminum scaffolding has several disadvantages, such as reduced strength compared to steel, making it less suitable for heavy-duty projects. It is also prone to bending or damage if overloaded. Additionally, aluminum scaffolding can be more expensive, which may not be cost-effective for large-scale or long-term projects.
Now that you know the basic disadvantages of aluminum scaffolding, let’s explore the specific issues related to its durability, cost, and strength that may impact your decision for construction projects.
Why Is Aluminum Scaffolding Less Durable Than Steel Scaffolding?
Concerned about durability? Aluminum scaffolding is less durable than steel because it has a lower tensile strength, making it more prone to damage or bending under heavy loads.
Aluminum scaffolding is less durable than steel due to its lower tensile strength. While it is lighter and easier to transport, aluminum can bend or warp when exposed to heavy loads or high stress, limiting its use in demanding construction projects.
Aluminum scaffolding is generally less durable than steel scaffolding because of its lower tensile strength. Steel can support heavier loads and withstand more stress, making it better suited for larger or more complex construction projects. Aluminum, while lightweight and easy to transport, can bend, warp, or become damaged under heavy loads, especially in high-stress applications. This makes aluminum scaffolding less ideal for projects that require significant weight-bearing capacity. Additionally, aluminum may be more susceptible to damage from impacts or rough handling on construction sites, further reducing its durability compared to steel.
Why Is Aluminum Scaffolding More Expensive Than Steel Scaffolding?
Budget concerns? Aluminum scaffolding is typically more expensive than steel due to its production costs, lightweight material, and added convenience, making it less cost-effective for larger projects.
Aluminum scaffolding is often more expensive than steel because aluminum is a lightweight, corrosion-resistant material, and its production costs are higher. While convenient for transport and assembly, the higher price tag may not be justifiable for long-term or large-scale projects that require high durability.
Aluminum scaffolding is more expensive than steel for several reasons. The production costs of aluminum are higher due to its lightweight nature and corrosion-resistant properties, which make it a desirable material for projects where mobility and easy transport are essential. However, this added convenience comes at a cost, and the price of aluminum scaffolding may not be justifiable for large-scale or long-term projects where strength and durability are more critical. Steel scaffolding, although heavier, is often the more cost-effective choice for projects requiring a high load-bearing capacity and long-term stability.
Is Aluminum Scaffolding Worth It?
Considering whether aluminum scaffolding is worth it? Aluminum scaffolding is worth it for projects requiring mobility and quick assembly, but its higher cost and lower strength may not be ideal for heavy-duty construction.
Aluminum scaffolding is worth it for lightweight or temporary projects where portability and ease of use are priorities. However, its higher price and lower strength compared to steel make it less suitable for heavy-duty or long-term construction projects that require maximum stability.
Aluminum scaffolding can be worth the investment depending on the type of project. It is highly valued for its lightweight, portable nature and ease of assembly, making it ideal for temporary structures, indoor projects, or construction work that requires frequent movement and relocation of scaffolding. However, for heavy-duty projects or long-term outdoor use, where higher load-bearing capacity and durability are essential, aluminum scaffolding may not be the best option. Its higher cost compared to steel may not be justified if the project requires significant strength or long-term use. In these cases, steel scaffolding is typically the better, more cost-effective choice.
Is Aluminum Scaffolding Safe for Heavy-Duty Construction?
Worried about safety? Aluminum scaffolding may not be the safest option for heavy-duty construction due to its lower load-bearing capacity and susceptibility to damage under heavy stress.
Aluminum scaffolding is less suitable for heavy-duty construction because it cannot support as much weight as steel. While it works well for smaller projects, aluminum is more prone to bending or collapsing under heavy loads, making it less safe for demanding construction environments.
While aluminum scaffolding is useful for light-duty or temporary projects, it is generally not recommended for heavy-duty construction. The lower load-bearing capacity of aluminum means that it cannot safely support the same heavy loads as steel scaffolding, making it more susceptible to bending, collapsing, or failing under stress. For projects requiring significant weight-bearing, such as high-rise construction or industrial work, steel scaffolding is the safer option. Although aluminum scaffolding is easier to move and assemble, its limitations in strength make it less appropriate for demanding construction environments where safety is a top priority.
Can Aluminum Scaffolding Be Used in Extreme Weather Conditions?
Working in harsh weather? Aluminum scaffolding, while corrosion-resistant, is less ideal for extreme weather due to its tendency to expand or contract in high temperatures, affecting its stability.
Aluminum scaffolding is not well-suited for extreme weather conditions. Although it resists corrosion, aluminum expands and contracts more than steel when exposed to high or low temperatures, which can lead to instability or structural issues in harsh climates.
Aluminum scaffolding may not be the best option for projects that take place in extreme weather conditions. While it has the advantage of being corrosion-resistant, it is more prone to expansion and contraction when exposed to significant temperature changes. This can cause instability and affect the structural integrity of the scaffolding. In high-temperature environments, aluminum can expand, while in extremely cold conditions, it may contract, leading to potential gaps or weakened connections. Steel scaffolding, on the other hand, is less affected by temperature fluctuations and is often the better choice for projects in areas with harsh weather conditions.
What Are Other Limitations of Aluminum Scaffolding?
Need to understand other limitations? Aluminum scaffolding, while convenient, has limitations in load-bearing capacity, impact resistance, and lifespan, which make it less effective for long-term or high-intensity projects.
Aluminum scaffolding also has other drawbacks, such as lower impact resistance, meaning it is more likely to be damaged from accidental hits. Additionally, its lifespan is shorter than steel, especially in high-intensity projects that demand long-term durability.
Apart from its lower strength and higher cost, aluminum scaffolding has other limitations. One of these is its lower impact resistance, meaning it is more likely to sustain damage from accidental bumps or hits on construction sites, which can compromise its stability. Additionally, aluminum scaffolding may have a shorter lifespan compared to steel when used in high-intensity projects that require long-term durability. While it is easy to assemble and move, these limitations make aluminum scaffolding less suitable for complex or demanding construction tasks that require high strength and long-term reliability.
Conclusion
In conclusion, aluminum scaffolding has several disadvantages, including reduced strength, higher costs, and lower durability compared to steel. While it is ideal for lightweight, temporary projects, aluminum scaffolding may not be suitable for heavy-duty construction or extreme weather conditions.